The installation process for a Mini Valve for Tubing in a tubing system typically involves the following steps:
Prepare the Tubing: Ensure that the tubing system is properly prepared before installing the Mini Valve. This may involve cutting the tubing to the desired length, deburring the edges, and ensuring that the tubing ends are clean and free from debris.
Select the Valve Position: Determine the appropriate location in the tubing system where the Mini Valve will be installed. Consider factors such as accessibility, required flow direction, and proximity to other components or connections.
Shut Off the Fluid Flow: Before installing the Mini Valve, ensure that the fluid flow in the tubing system is shut off. This can be done by closing any upstream valves or shutting down the fluid source.
Insert the Valve: Insert the Mini Valve into the tubing system by aligning the valve’s inlet and outlet ports with the tubing ends. Ensure that the valve is oriented correctly to maintain the desired flow direction.
Connect the Tubing: Once the valve is in position, connect the tubing ends to the valve ports. Depending on the type of Mini Valve and tubing system, this can be accomplished through various methods such as compression fittings, barb fittings, or push-to-connect fittings. Follow the manufacturer’s instructions for the specific valve and fitting type being used.
Tighten the Connections: Secure the tubing connections to the Mini Valve by tightening the fittings or clamps. Ensure that the connections are snug but not over-tightened, as this can damage the tubing or fittings.
Test for Leaks: After the connections are made, it is essential to test the system for any leaks. Slowly turn on the fluid flow and observe the installed Mini Valve and its connections for any signs of leakage. If leaks are detected, tighten the connections as needed or replace any faulty components.
Operate and Verify Functionality: Once the Mini Valve is installed and leak-free, operate the valve to verify its functionality. Open and close the valve to ensure smooth operation and proper flow control. Verify that the valve effectively shuts off the fluid flow when closed and allows flow when open.
System Integration: If there are other components or fittings in the tubing system, ensure that the Mini Valve is integrated properly with them. Mini Valve For Tubing This may involve connecting additional tubing, fittings, or adapters to achieve the desired system configuration.
System Testing: Finally, perform a comprehensive testing of the tubing system with the Mini Valve installed. This may include testing the flow rate, pressure, and overall system performance to ensure that the valve operates as intended and meets the system requirements.
It is important to follow the specific instructions provided by the Mini Valve manufacturer for installation, as the process may vary depending on the valve’s design and model. Additionally, adhere to standard safety practices and consult valve experts or professionals if needed.
How does a Mini Valve for Tubing differ from standard-sized valves?
A Mini Valve for Tubing differs from standard-sized valves in several ways:
Size: As the name suggests, a Mini Valve for Tubing is smaller in size compared to standard-sized valves. It is designed to fit and operate within smaller tubing systems where space is limited. The compact size of the mini valve allows for easy installation in tight or confined spaces.
Flow Capacity: Due to their smaller size, Mini Valves for Tubing generally have a lower flow capacity compared to standard-sized valves. They are typically designed for applications with lower flow rates or systems with smaller tubing diameters.
Pressure Rating: Mini Valves for Tubing often have a lower pressure rating compared to larger valves. They are typically suitable for low to moderate pressure applications. It is important to consider the pressure requirements of the specific application and select a mini valve with an appropriate pressure rating.
Actuation Method: Mini Valves for Tubing can be operated using various actuation methods, including manual, mechanical, or pneumatic actuation. The actuation mechanism may be different from standard-sized valves due to the size constraints. Manual actuation options such as knobs, levers, or handles are commonly used for mini valves.
Material Selection: Mini Valves for Tubing are available in different materials, just like standard-sized valves. However, due to their smaller size, certain materials may be more commonly used in mini valves, such as plastics or lightweight metals. The material selection ensures the valve’s durability and compatibility with the specific application requirements.
Connection Type: Mini Valves for Tubing may have specific connection types suitable for smaller tubing sizes. They often feature fittings or connections designed to accommodate the smaller diameter tubing commonly used in mini valve applications, such as compression fittings or push-to-connect fittings.
Application Scope: Mini Valves for Tubing are typically used in applications where a smaller flow control or shut-off valve is required within a tubing system. They are commonly found in medical devices, laboratory equipment, small-scale fluid handling systems, or other applications where space and flow rate constraints exist.
Despite these differences, mini valves for tubing serve a similar purpose as standard-sized valves, which is to control the flow of fluid or gases within a system. The specific design and specifications of the mini valve are tailored to meet the requirements of smaller-scale applications.
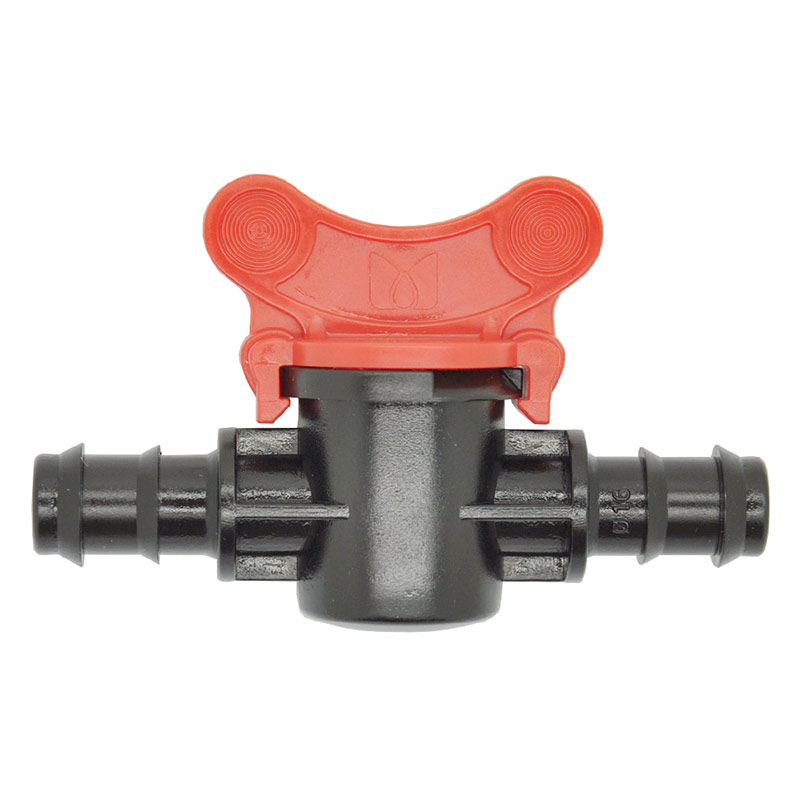